Project Status
Week of 02-06-19
Project is: ON TRACK
Although we have run into a few setbacks, primarily in the circuit design, we are still on track to be completed by the deadline.
Issues / Extra progress from last week:
​
-
Evaluation of the spot welder and assembly of the cells lead to a more traditional approach
-
The battery pack was redesigned using interlocking 3D printed holders. These 6x1 battery holders will be configured to fit within an aluminum waterproof enclosure.
-
Sourcing a company to make motor driver PCB
-
Good price and reasonable turn around​ time
-
Accomplished this week:
Battery pack design:
-
​Battery pack was redesigned using a modular 6x1 frame.
-
BMS position was determined andwiring was laid out
-
New welded enclosure was designed with removable cover

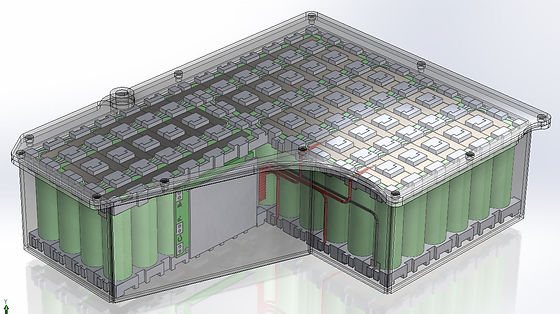


Motor Mount adjustments:
-
The 48v BLDC motor was 1mm larger in diameter than specified on the data sheet.​
-
Internal Diameter was increased 1mm to compensate for larger outside diameter of the motor
-
Clamp feature was rotated clockwise 75 degrees to allow more room for the battery and better access for tools

Component fit checks:
-
The 48v BLDC motor was a tight squeeze due to the 1mm interference on the OD of the motor
-
The lead on the back side will need a guard and clocked to be out of the way.
-
The throttle potentiometer installed with no issues, the wires are long enough to reach the rear of the bike.

Electrical
-
Continued circuit design
-
Began preliminary circuit testing in MultiSim
-
Began writing code for eBike controller


Goals for next week:
-
Complete circuit design
-
Begin sourcing motor driver PCB
-
Continue code for eBike controller
-
build a test battery pack
-
coordinate with Jeremy Cornwall to use the Randolph campus waterjet
-
Source aluminum plate needed for parts
-
Verify round stock for spacers, turned on lathe at Williston campus
References:
-
ebike school https://www.youtube.com/watch?v=u-4mKh1WaLo&t=463s